The Future of IIoT
As the industrial internet of things (IIoT) advances, it is generating unprecedented opportunities for organizations–from the SMB to the multinational enterprise–to optimize operations, improve customer experiences, and drive significant revenue gains.
The future of IIoT will include more emphasis on predictive maintenance, enhanced device communication, and more affordable access for companies of all sizes to tap into the business benefits of the connected facility. Among those benefits are productivity gains, cost savings, immediate control, and quick detection of issues and opportunities.
In this article, we’ll discuss what the future of the industrial IoT has in store and how businesses can prepare themselves for their own “digital transformation.”
IIoT’s Impact on Product Development
The IIoT is already changing the game for product development. According to Vodafone, more than a third of today’s companies are already leveraging IoT devices to improve operating costs, drive efficiencies, and optimize existing processes.
Microsoft’s 2019 IoT Signals report lays out how manufacturing companies are currently using IIoT solutions in the product development process and where things are headed. Here’s how they break it down:
- Development. Organizations can use 3D modeling systems, digital twins, as well as real-time production and equipment data to create new concepts and inform product specs without wasting physical resources.
- Testing. From there, companies might send those specs to an overseas vendor to 3D print a test batch.
- Validation & Quality Assurance. Next, organizations might then use real-time data to test the batch for durability and performance quality, sending information to connected machines at vendor sites.
- Mass Production & Product Assembly. Production equipment is embedded with sensors to help organizations determine maintenance needs, establish an ETA for bringing products to market, etc.
- Distribution. Final products are shipped to consumers and sellers, along with inventory tracking sensors.
- Future Use Cases. Microsoft predicts that we’ll soon see more and more companies move away from hard-wired IoT-connected production equipment to WiFi-based solutions. They also mention that we’ll start to see organizations expand their validation practice to a broader range of product lines/use cases, as they develop a replicable process.
How Will IIoT Work With Other Emerging Technologies?
If you want a glimpse inside the future of IIoT, looking at some of the top industrial IoT trends of 2020 is a good place to start.
Here’s a look at some emerging IIoT trends within the industrial internet of things space:
IIoT Manufacturing as a Service
As with just about everything in today’s cloud-connected world, the concept of IoT as a Service (IoTaaS) is an emerging trend among tech-forward firms. IoTaaS is a term used to describe the process of managing, controlling, and delivering connected devices as a service. IoTaaS platforms offer APIs for a wide range of devices, sensors, and actuators, giving users the ability to quickly set up a complex ecosystem of heterogeneous “things” and start capturing real-time insights from all connected data sources.
In an industrial context, IIoT as a service allows organizations to easily manage and deploy connected systems, while a third-party provider handles device management, advanced analytics, security, updates, and more.
While organizations will need to have a basic understanding of how vendors manage data and security, IoTaaS providers stand to make smart manufacturing accessible for a wider range of organizations–including those with limited IT, OT, or cloud expertise.
The idea is, by offering this “plug-and-play” solution, organizations can save the time and resources involved with, say, building a cloud backend for a specific hardware device. Instead, they can reduce operating costs, get products to market faster, and scale an entire system in a matter of clicks.
Mix Of Cloud & Edge Computing
According to the Industrial Internet Consortium (IIC), 70% of senior IT executives say that the ability to correlate data from any connected source into a common data model is the most significant benefit the industrial IoT has to offer.
As the IIoT expands, data is being generated by more and more sources, and as a result, many organizations require computing power that spans several locations. Organizations will need to embrace hybrid models (cloud edge) to make the most of all of this data–enabling real-time data analytics where needed, as well as scalable, cost-effective storage solutions.
We discuss this in more detail here. In short, edge computing allows organizations to process data from sensors and equipment locally and in real-time. Edge computing is emerging as a solution to the latency issues common in cloud-based solutions, allowing organizations to avoid delays and lag time that lead to safety issues, production hiccups, and open the door to security threats.
The cloud, on the other hand, allows companies an affordable, scalable solution for storing data long-term. It’s also ideal for the historical analysis involved in activities like demand forecasting, production optimization, and supply chain management.
Additionally, cloud-based solutions that process massive data sets allow organizations to create a deep learning model that can be applied at the edge. For example, AI can be trained to recognize patterns and detect threats in the cloud. Then later, that model can be embedded into the production process to capture insights and respond to threats in real-time.
Predictive Maintenance
Another IIoT trend that continues to rise is the use of IIoT data in predictive maintenance. While early adopters have long been using IoT solutions for asset management tasks, this application is evolving thanks, in part, to AI applications, augmented reality, and digital twins.
Embedded sensors now allow factories to measure energy consumption and machines to reduce waste and optimize production processes. They can also feed information collected from various machines–across several locations–and send those insights directly to the production line, allowing manufacturers to make improvements on the fly.
Digital twins are virtual representations of equipment, devices, processes, products, or any other asset that exists within the physical world. While the concept of digital twins has been around for a few years now, the technology is evolving.
Organizations can create digital representations of what’s happening in real-time, in real life, thanks to digital twins. This capability gives organizations the ability to monitor and control physical assets remotely, without ever physically interacting with them, analyze a range of scenarios, and act on insights generated from connected assets.
AR and the IoT might be used to ensure safer, more accurate repair jobs. Connecting IIoT data from a particular asset and merging that information with digitized instructions and augmented reality application allows front line workers to leverage that cyber-physical connection.
Location Tracking – Tools, Equipment, & Inventory
Another trend that offers a glimpse into the future of IIoT is location-tracking. While geo-location capabilities have been around for a while, the space is continuing to evolve. In the past, location tracking was largely limited to GPS, which lacks power efficiency and indoor coverage.
Today, organizations can use a wide range of location tracking tools, including RFID tags that track the movement of inventory at the shelf-level and connect with a company’s ERP. Or, long-range charging solutions that support remote asset monitoring and greater efficiency.
Additionally, organizations can combine location-tracking solutions with other technologies. For example, manufacturing companies can manage their physical assets by monitoring their location with GPS-enabled sensors and using AI to track environmental and security conditions.
Alternatively, construction workers might use a sensory system to keep tabs on equipment located on large job sites, tracking assets with GPS while outdoors. When indoors, teams can switch to an indoor AI-based location system supported by WiFi or other sensors that can provide more accurate indoor positioning. This can reduce the time workers or autonomous robots spend trying to locate a particular machine by leveraging intelligence at the Edge.
Near and Long Term Industrial Automation
By some estimates, the COVID-19 pandemic is likely to increase demand for industrial automation and digitization processes in the near-term, as part of a disaster management plan, which, of course, will have long-term effects on how industrial firms operate in the future.
How Should Businesses Prepare for the Future of IIoT?
Getting the biggest returns on your IIoT investments begins with understanding how it can make a difference in your business. What will your stakeholders gain by embracing predictive maintenance? How might digital twins help the C-suite make better decisions? What insights will processing OT data at the edge deliver?
As your business prepares to adopt IIoT technologies or improve on existing solutions, consider your business objectives, your company’s readiness, your existing capabilities, and what you’ll need to put in place to bring your system into the future.
[adinserter name=”IIoT Closing”]
Recent blog posts
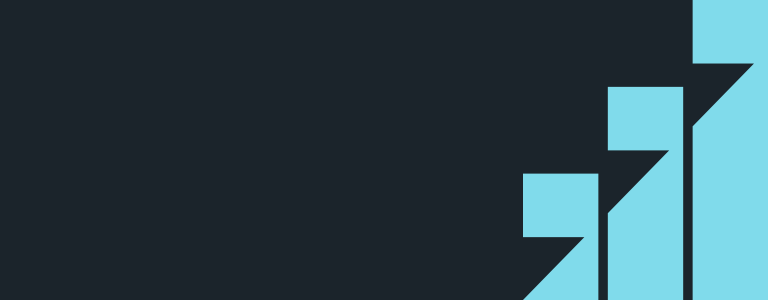
Stay in Touch
Keep your competitive edge – subscribe to our newsletter for updates on emerging software engineering, data and AI, and cloud technology trends.