The State of Industrial Internet of Things
IIoT is increasingly taking up more space in industrial environments, improving operations, resource utilization, inventory management, and more through sensors, smart machinery, and, like all things Industry 4.0, new opportunities for collecting mountains of data.
A survey by Microsoft found that 85% of companies have at least one IoT project in the works, and a recent forecast by Million Insights predicted that the Industrial Internet of Things (IIoT) could reach a whopping $992 billion in global spending by 2025.
In this article, we’ll explore the key trends and insights shaping the current state of IIoT.
How IIoT is Improving Operational Effectiveness
IIoT in manufacturing helps companies optimize their operations via smart machinery, sensors, RFID, and other connected technologies—so it comes as no surprise that adoption in this space continues to trend upward.
IDC data revealed that in 2019, manufacturing operations topped the list of IoT use cases with the most investment. In a report by the American Society for Quality (ASQ), manufacturing companies that have digitized their processes report an 82% increase in overall efficiency, 49% fewer reported product defects, and a 45% increase in customer satisfaction.
In these next few sections, we’ll look at some specific areas where IoT solutions are driving operational efficiency across a wide range of companies.
Transforming Legacy Systems
One of the biggest opportunities offered by IIoT is its ability to modernize legacy systems. According to McKinsey, the average factory is 25 years old, operating with disconnected machines that are, on average, about nine years old.
That lack of connectivity makes it challenging to implement organization-wide monitoring and controls. However, new solutions known as integration platforms allow manufacturers to retrofit older machines with sensors, presenting a cost-effective way to optimize existing assets. These platforms function almost like an adaptor for older machinery, collecting data from wire-based industrial protocols, then forwarding those insights to a remote control center via long-range Wi-Fi.
It’s also worth pointing out that innovation extends beyond the machines themselves, with IIoT devices bringing intelligence into analog processes. For example, a few different companies have developed connected handhelds and helmets that assist technicians on the job. These tools walk workers through checklists and repair processes, reducing the risk of injury or error during routine tasks.
Greater Energy Efficiency
In a study published by Panoramic Power, about 77% of organizations report that their main source of energy consumption data comes from monthly power bills or energy monitoring tools with limited visibility into usage analytics.
IoT changes the game allowing manufacturers to track energy usage patterns by outfitting machinery with sensors.
Organizations now have unprecedented visibility into energy consumption and can use sensors to detect anomalies, off-hours consumption, wasteful behaviors, and unusual usage patterns. That information might then be used to inform predictive maintenance schedules or optimize production processes.
Data Analytics Get Smarter
Data analytics as a concept isn’t exactly on the cutting edge of innovation in any industry at this point. As sectors like manufacturing, energy, utilities, and aerospace increasingly embrace IoT-powered sensors and wireless technologies, it’s becoming clear that the real promise of IIoT is all about analytics.
These connected systems generate a TON of data, but manufacturers need to be able to effectively extract the right insights and put them to good use. As such, the demand for IoT analytics tools is on the rise—with companies like SAP, Teradata, and SAS offering AI and machine-learning tools to help organizations manage the data deluge.
This new wave of advanced analytics software is breaking down data silos and bringing real-time data from all connected systems—from the factory floor to the job site—together in one place. Leaders can see data from a whole range of touchpoints to get a holistic view of how their business is performing—and use data-driven insights to inform their strategy.
Cobots Bring Connected Support to Human Workers
No, “cobots” is not a typo, rather it’s a shortened term for “collaborative robots,” another rising trend defining the state of the industrial internet of things, with investments expected to hit $12.3B by 2025.
While the concept of industrial robots isn’t exactly new, cobots are a bit different.
For one, traditional robots aren’t designed with human safety as a top priority. While you’ll generally have some safeguards in place, industrial robots are often found caged off from their human colleagues.
Cobots are lightweight and designed to work right alongside human workers. Like other IoT technologies, cobots are equipped with sensors, which render them location, people, and context-aware. While use cases range from the coffee counter to the operating table, cobots are well-suited for a diverse range of manufacturing activities including:
- Machine tending
- Packaging and palletizing
- Finishing tasks like grinding or polishing
- Quality assurance testing
Digital Twins are Gaining Traction
Another feature defining the state of IIoT? Digital twins.
Digital twins are virtual replicas of physical devices that allow IT teams and data scientists to use to run simulations before building those devices out in the real world.
As it stands, a growing number of industrial firms are using IoT solutions to reproduce their assets digitally. This way, companies can take real-world data (like temperature, condition, location, etc.) from sensors attached to each physical asset and run it through a series of scenarios to learn how objects respond to change.
Digital twins are gaining traction within the IIoT landscape, as it allows them to incorporate process data, enabling them to reach accurate insights and address operational inefficiencies.
Gartner reports that 24% of enterprises are already using digital twins, while another 42% say they’ll likely adopt this technology within the next three years.
Edge Computing is Shaking Up the IIoT Landscape
Edge computing is changing the state of the Industrial Internet of Things (IIoT), transforming how organizations handle, process, and share data collected from connected networks of devices.
Until recently, cloud computing was the go-to solution for controlling connected data and devices. However, as more organizations embrace IIoT devices and sensors, there will soon be a LOT more data, and organizations will need a better way to monitor, manage, and protect all of that information.
As it stands, cloud-based systems can’t keep up, presenting problems like latency issues and security risks.
The benefit of edge computing is, it allows IoT devices to process data closer to the source in what’s called edge data centers. Because the data doesn’t need to travel as far as it would under cloud-based architecture, organizations can monitor data in real-time–at scale.
Adoption Hurdles and Common Pitfalls
While many organizations are realizing the benefits of IIoT, many more are struggling to identify the right use case for these new technologies. According to a survey by PwC’s German branch, 91% of respondents say they are investing in digital transformation, yet only 6% report being “fully digitized.”
While there are many reasons an organization might struggle to implement IIoT solutions successfully, here are a few examples experts have recently pointed out:
- Lack of Expertise. Gartner found that IIoT initiatives are often unpredictable because companies often fail to define the right metrics and don’t use the technology needed to drive continuous improvements.
- Vendors. Bain & Company reported that vendors and customers often don’t value the same use cases. For example, customers might be eager to embrace augmented reality tools for maintenance and training, while vendors are more focused on promoting predictive maintenance.
- Security Concerns. Microsoft found that 97% of companies have security concerns related to IoT adoption. Given the sheer volume of data generated by connected IoT systems, manufacturers are concerned about protecting internal and customer data amidst increased security threats.
- Unclear ROI. Finally, companies are unsure of whether investing in connected devices and systems will deliver meaningful returns.
As we’ve discussed in the context of microservices and DevOps, any transformation without an informed use case and measurable set of objectives are likely to fail.
IIoT implementation tracks with that logic, and as such, it’s important to stress that organizations should never buy up a bunch of cobots or outfit their machines with sensors just because it’s becoming popular.
Are You Keeping Pace with Today’s IIoT Landscape?
In 2020, the current state of IIoT suggests that we’re on the verge of widespread adoption.
Connected systems are moving beyond proof-of-concept or sci-fi material and becoming an essential part of the industrial landscape and organizations will need to address quickly.
[adinserter name=”IIoT Closing”]
Recent blog posts
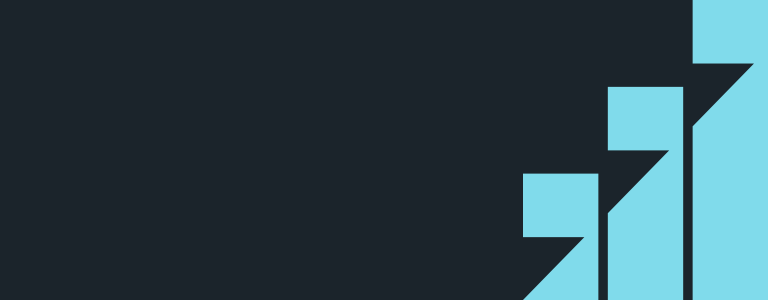
Stay in Touch
Keep your competitive edge – subscribe to our newsletter for updates on emerging software engineering, data and AI, and cloud technology trends.